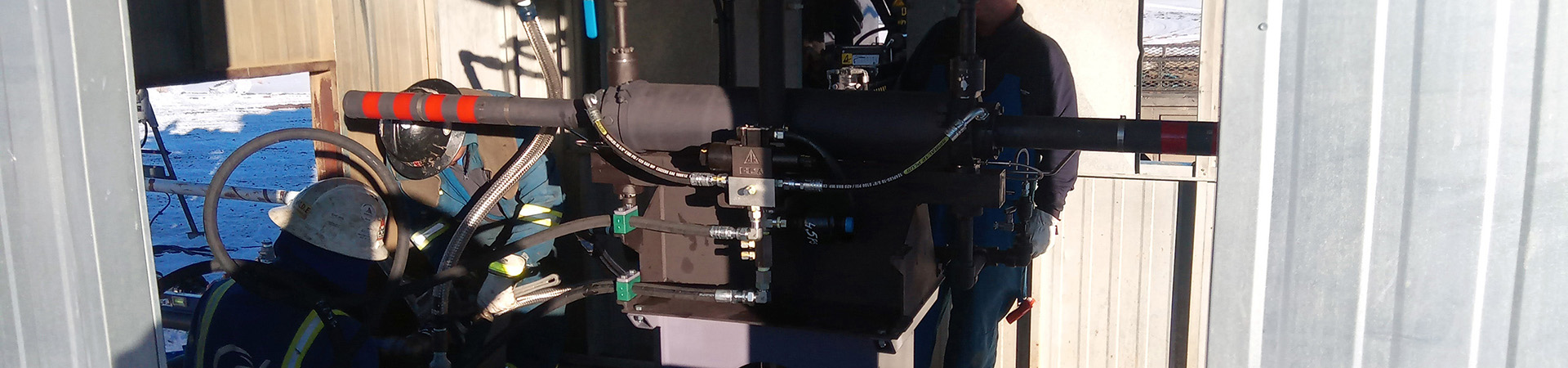
Preventive Maintenance | Scheduled Site Visits | Upgrades | Detailed Maintenance Records | 24/7 On-Call Service | OEM Parts
Our Goal:
Reduce your cost of ownership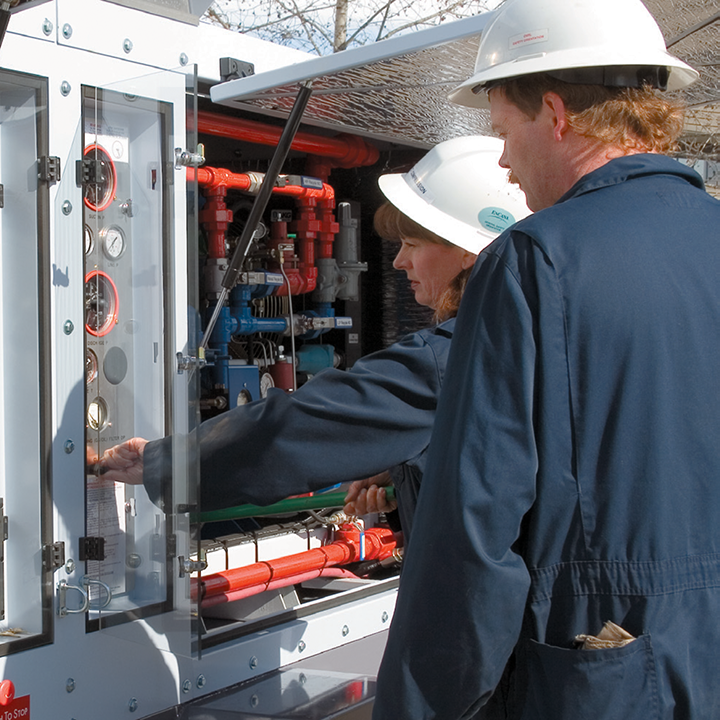
How?
Less downtime due to failuresInspection Program – We use a model specific checklist which is continuously updated based on experience.
Upgrade Program – When widespread issues are found, affecting performance and durability, an engineered solution is developed to remove that problem.
Help Line – We have over the phone support for operators. This allows us to properly diagnose the problem so the mechanic going to site knows what to fix immediately. We also can advise the operator how to fix or keep the unit running until we can get on site.
Lower cost to repair
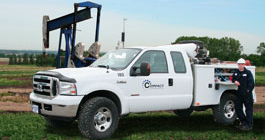
Do work faster – we have the most experience with our product.
Stocked parts - Parts that aren’t on the truck are usually large and will be carried if that is the suspected problem.
No excessive markup on parts – remove the middleman.
Production optimization
Our mechanics work directly with our engineering department to optimize the performance of the compressor.
No Hassle Service Plan - NHSP
Providing solutions for increased oil production with predictable service cost and No Hassle
What is the No Hassle Service Plan?
The NHSP is an all-inclusive fixed cost service plan for Hydraulic Casing Gas compressors (HCGs).
Why we offer a No Hassle Service Plan?
Our core business is casing gas compressors – design, build and service. The size of the Casing Gas Compression market is driven by economics, therefore lower capital and op cost, along with less hassle, results in a larger market. We realized that in order to grow the market, in addition to a new compression element, a new approach to service was needed – the No Hassle Service Plan and SkyView monitoring system. We see all unusual process and operational issues affecting reliability and service cost, and design and implement hardware and processes to minimize or eliminate their negative effects. The result, lower costs and less hassle leads to more sales.
How can our customers benefit from the NHSP?
|
Maximize Uptime |
Our customers benefit from increased oil production at minimal cost and No Hassle |
What does the all-inclusive No Hassle Service Plan actually include?
Service |
All compressor parts, fluids and labour for routine service, repair, and overhauls |
Performance Changes |
Thought you needed a low ΔP high volume cylinder and on installation you find out you really need a high ΔP low volume cylinder? Cylinder changes are included in the NHSP. |
Monitoring |
SkyView, our reporting system, identifies and collects data from HCGs, allowing us to diagnose and avert potential interruptions before they occur. Customers can access live performance data through secure server |
Upgrades |
If there are endemic operational or service issues, we design these imperfections out and implement upgrades across the existing fleet. |
Travel |
Travel time and mileage to our established service areas (Calgary, Grande Prairie, Swift Current and Stoughton). Outside our regular service areas, a low fixed annual Remote Surcharge is applied; which presumes help from the customer for simple tasks. If required, we will have a Service Tech on site the next working day. |
SkyView - Live Monitoring
24/7 Exclusive Access to Compressor Status - only available with our No Hassle Service Plan
In 2018, CCI implemented SkyView, an IoT Platform that links HCG sensors, telemetry and a front-end so that HCG condition can be accessed on any internet capable device. SkyView is used as a predictive planning tool by field service technicians and dramatically shortens the response time to remedy distressed units. Additionally, customers have access to SkyView that can help optimize well performance.
As a result of customer feedback and our own experience, we continue to make changes to the SkyView system to improve capabilities and ease of use. Having live status, suction and discharge pressure data available online eliminates operators making daily trips to wells to record pressure readings, increasing their efficient use of time and reducing driving exposure.
Used by CCI service technicians to:
- Diagnose and avert potential issues
- Maximize equipment uptime
- Reduce costs due to unnecessary visits
- Reduce costs due to catastrophic failure
Used by customers to:
- Monitor equipment status
- Monitor current compressor pressures and trends
An overview of compressor status in field
View all suction and discharge pressures at a single glance. With just a single click, access detailed information.
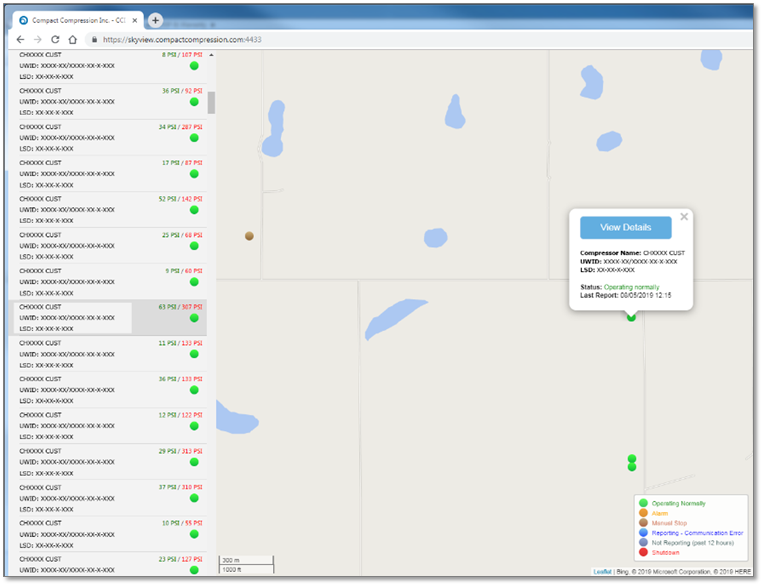
Access up to a 90-day snapshot of the compressor's pressure performance
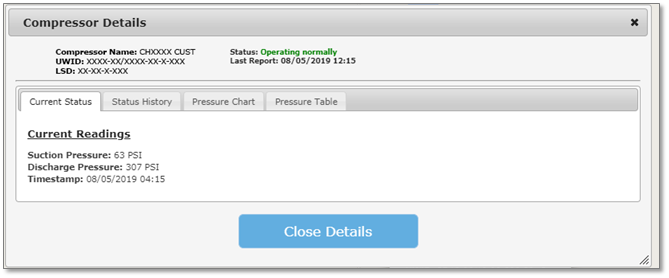
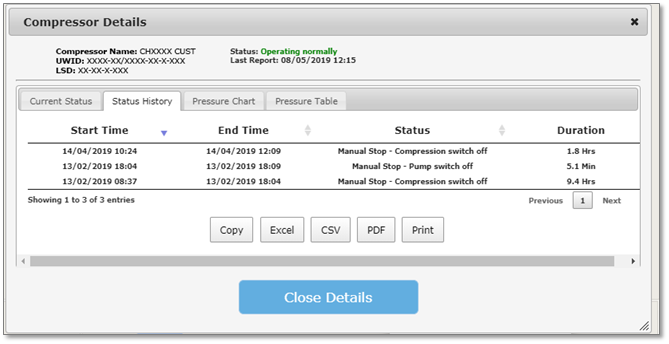
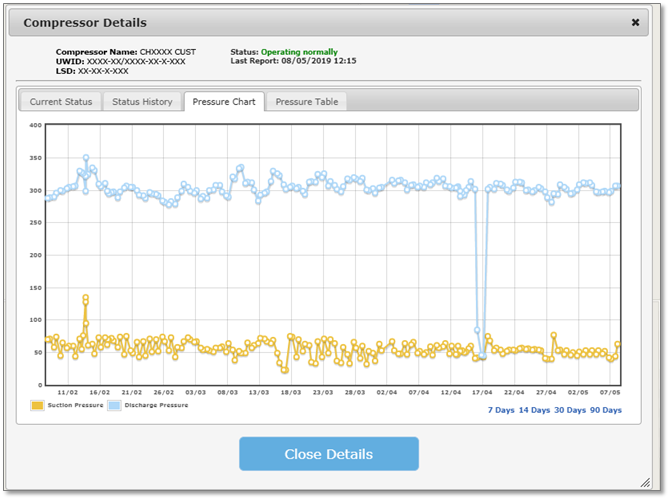
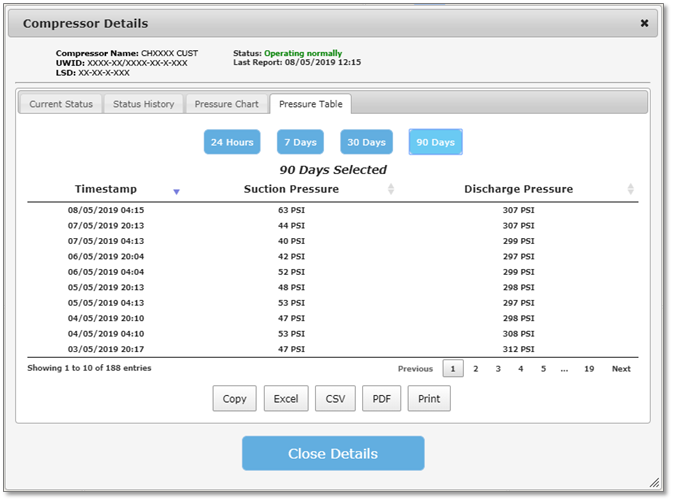
Service Locations
Service locations conveniently located throughout the prairies.
Field Service Technicians
Southern Alberta
Jason Huntley
Cell: 1-403-975-8602
jhuntley@compactcompression.com
Lee Stevens
Cell: 1-403-826-4231
lstevens@compactcompression.com
Northern Alberta
Jason Huntley
Cell: 1-403-975-8602
jhuntley@compactcompression.com
Northern Alberta / British Columbia
Jamie Best (Grande Prairie)
Cell: 1-780-903-5960
mtranberg@compactcompression.com
Rylind Smith (Grande Prairie)
Cell: 1-403-899-3291
mtranberg@compactcompression.com
Saskatchewan (SW)
Jonathan Farewell
Cell: 1-306-294-7237
jfarewell@compactcompression.com
Saskatchewan (SW)
Tyler Boiteau
Cell: 1-306-750-6005
tboiteau@compactcompression.com
Saskatchewan (SE) / Manitoba
Chris Carlson
Cell: 1-306-421-6420
ccarlson@compactcompression.com
Robert Carlson
Cell: 1-306-897-5060
rcarlson@compactcompression.com
Vince Gilroy
Cell: 1-306-421-2716
vgilroy@compactcompression.com
Mike Swanson
Cell: 1-306-897-5003
mswanson@compactcompression.com