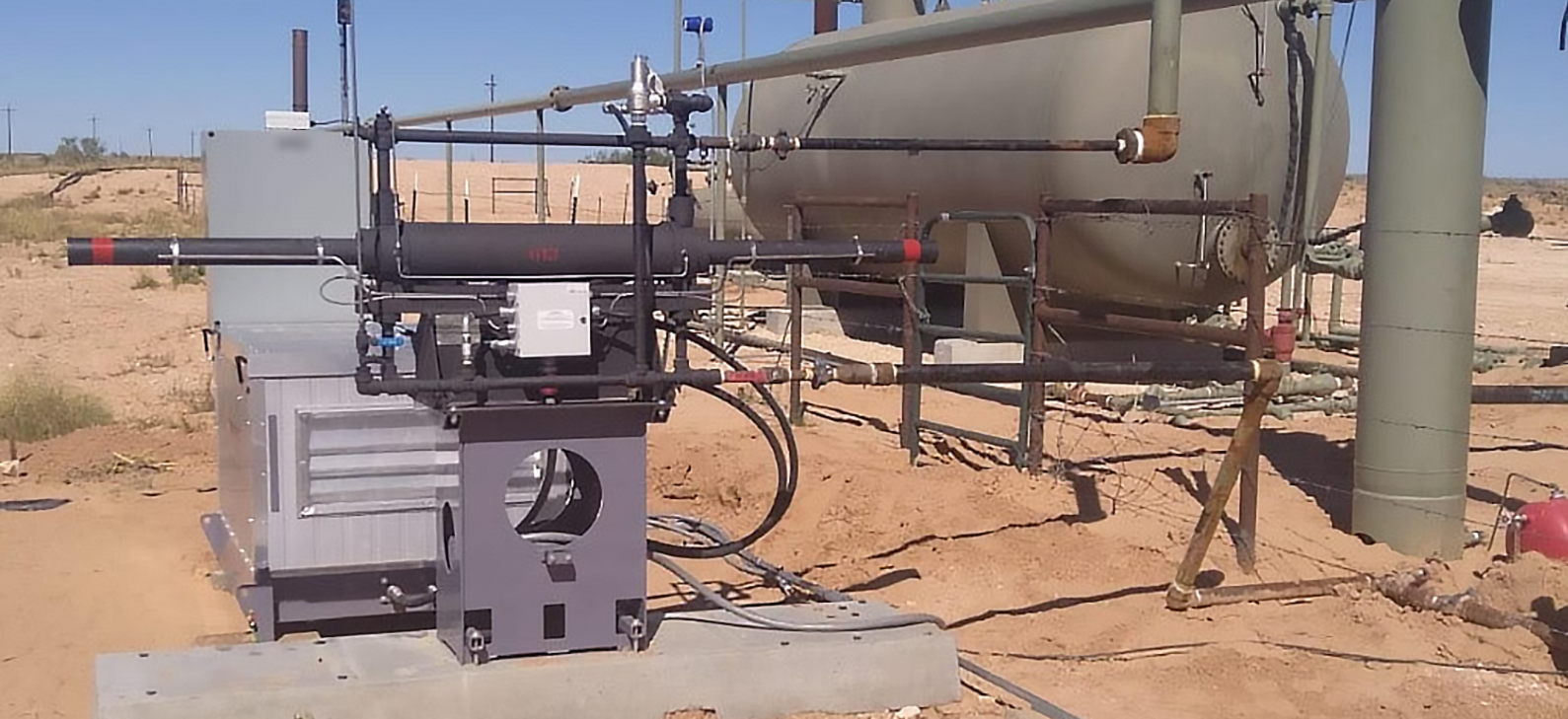
Extremely Tight Suction Pressure Control | Compressor Processes Liquids | No Pneumatic Valves or Vessels | Automated Capacity Control | SkyView Real-Time Reporting | Set & Forget PLC Control | Best-In-Class Reliability
Vapor Recovery has become a critical requirement for today’s Oil & Gas producers to meet regulatory emissions standards and capture valuable methane and longer chain hydrocarbons, CO2, VOC’s, and hazardous air pollutants while preventing their release to the atmosphere. Eliminating flaring, incinerating, and venting is also essential. Compact Compression’s line of Vapor Recovery Units (VRUs) and Vapor Control Systems offer a range of solutions for environmental vapor recovery and emission control in the Oil & Gas industry.
Our Gas Recovery Units (GRUs) and Gas Recovery Systems are designed for gas capture from storage tanks, treaters, separators, and seal vents on large reciprocating compressors used in natural gas transmission and throughout gas storage operations. With our Tank Vapor Recovery technology, our VRUs and Vapor Recovery Systems can capture and recover vapors from storage tanks, reducing emissions and generating additional revenue.
Compact Compression’s Hydraulic Vapor Recovery Compression Systems (HVR) are developed from our proven HCG design and offer a low cost of ownership and a quick return on investment often achieved in a matter of weeks.
The Compact Compression Hydraulic Vapor Recovery (HVR) Compressor Philosophy
We have focused on 3 primary technical objectives when designing our systems:
1. Compression of saturated hydrocarbon gas in the presence of liquids
2. Eliminate the need for inlet liquids separation
3. Eliminate the need for costly scheduled maintenance
Applications
Storage Tanks ◆ Treaters ◆ Separators ◆ Transmission ◆ Gas Storage Operations ◆ Seal Vents on Large Reciprocating Compressors used in Natural Gas
To find out more, read Solving Common Vapor Recovery Challenges with Compact Compression's HGC and HVR Technology.
Features
- The HVR is ideally suited for wet or dry VRU applications! Liquids, including slugs, are processed right in the compression cylinder and no inlet liquid handling equipment is required.
- Extremely tight suction pressure control. The HVR uses a high-resolution suction pressure transmitter to allow the system to control suction pressure to within 1 inH2O (0.6 oz/in2) of target pressure.
Click to view HVR Suction Pressure Control Testing
HVR qualification testing carried out by CCI Engineering confirmed that even at a low suction volume (94 ft3), our HVR systems are capable of controlling suction pressure with extremely high accuracy and precision, to within 1 inH20 of the setpoint.
- 100% turndown capability. The HVR pauses the compression stroke when it senses the supply of gas to the compressor stops, resumes when gas supply resumes.
- HVR self-regulated capacity control. The compressor only needs to be sized for maximum expected flowrate and the unit will auto-adjust to volumes below the maximum.
- No VFD
- Unit auto-restarts after power loss
- No fugitive emissions. Suction and discharge pipe spools are made of threaded joints, compressor seals are vented to compressor suction so there is no opportunity to vent to atmosphere.
- Sour service capability. Optional NACE compliant PSV and heavy wall piping for sour service.
Click to see how our HVR product line is suitable for sour service
HYDRAULIC VAPOR RECOVERY COMPRESSORS FOR SOUR SERVICE
The Hydraulic Vapor Recovery Compressor product line is suitable for sour gas service. All process wetted structural or pressure containing metal parts are constructed of low-carbon steels that comply with the NACE MR0175 sour service standard. Chemical composition and hardness meet the requirements for usage in SSC region 3, as defined by part 2 of the standard. All elastomers and polymers used for seals are materials selected for resistance to sour gas and acid attack. The gas seal distance pieces are vented back to suction to ensure gas only needs to be vented when service work on the compression element is required. All process piping has been designed to ASME B31.3 Normal service, 1500 psi MAWP, and all units are hydrostatic tested, including the compression cylinder. For service greater than 2000 ppm, Compact Compression offers optional corrosive service piping for increased corrosion allowance via thicker wall pipe and fittings.
- SkyView. Condition-based monitoring via SkyView leads to low-cost, highly efficient demand-based maintenance.
- Communications with customer systems. PLC easily interfaces with customer control systems via Modbus, Ethernet / IP protocols or other means as required.
- Compression cylinder field replacement. Compression cylinders are fully field-replaceable and have an average field life of 2 years prior to rebuild.
- Low maintenance. Average maintenance interval is 2 visits / year (across 1,000 units)
- Low hydraulic oil consumption. ~0.025 gal/d - oil top up twice / year
- Highly experienced engineering support. >150 performance upgrades implemented over 5 years.
- HVR configurability & versatility. Hydraulic Vapor Recovery models are configurable for a wide operating envelope to meet ΔP and production rate requirements.
- Wide operating ambient temperature range. -40°F to 130°F (-40°C to 55°C)
- Best in class reliability! >99% uptime.
- Low cost of installation and ownership
- Availability & delivery timing. For most models 4 to 8 weeks delivery.
Options
- Power Pack Enclosure
- Hydraulic Heat Trace
- Inlet Particle Filter
- Configurable for varying operating DP and flow (Options for motor, hydraulic pump, compression cylinder size, multi-stage units)
- Electric or gas drive available
- Skid or trailer mounted units
Hydraulic Vapor Recovery (HVR) System Model Comparison
COMPRESSION CYLINDER
506
5" (11.2 cm)
MAX ΔP
110 psi
758 kPa
CAPACITY
Suction @ 20 psi
50 mscf/d
1416 m3/d
COMPRESSION CYLINDER
613
6" (15.2 cm)
MAX ΔP
225 psi
1551 kPa
CAPACITY
Suction @ 20 psi
73 mscf/d
2067 m3/d
COMPRESSION CYLINDER
1016
10" (25.4 cm)
MAX ΔP
125 psi
862 kPa
CAPACITY
Suction @ 20 psi
168 mscf/d
4757 m3/d
HVR 50
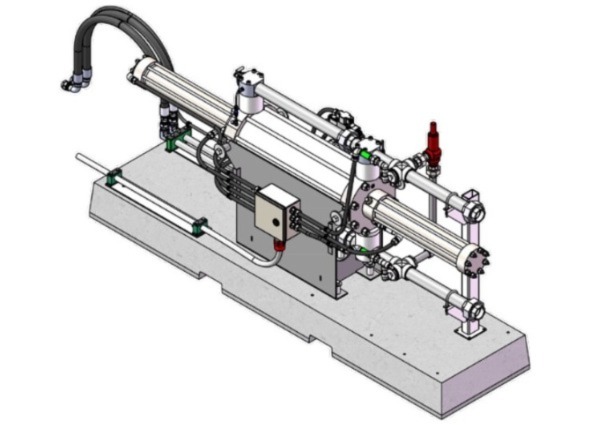
COMPRESSION CYLINDER
LOW PRESSURE
1020
10" (25.4 cm)MEDIUM PRESSURE
1022
10" (25.4 cm)
MAX ΔP
LOW PRESSURE
190 psi
1069 kPaMEDIUM PRESSURE
225 psi
1551 kPa
CAPACITY
Suction @ 20 psi
LOW PRESSURE
209 mscf/d
5918 m3/dMEDIUM PRESSURE
164 mscf/d
4644 m3/d
HVR 100
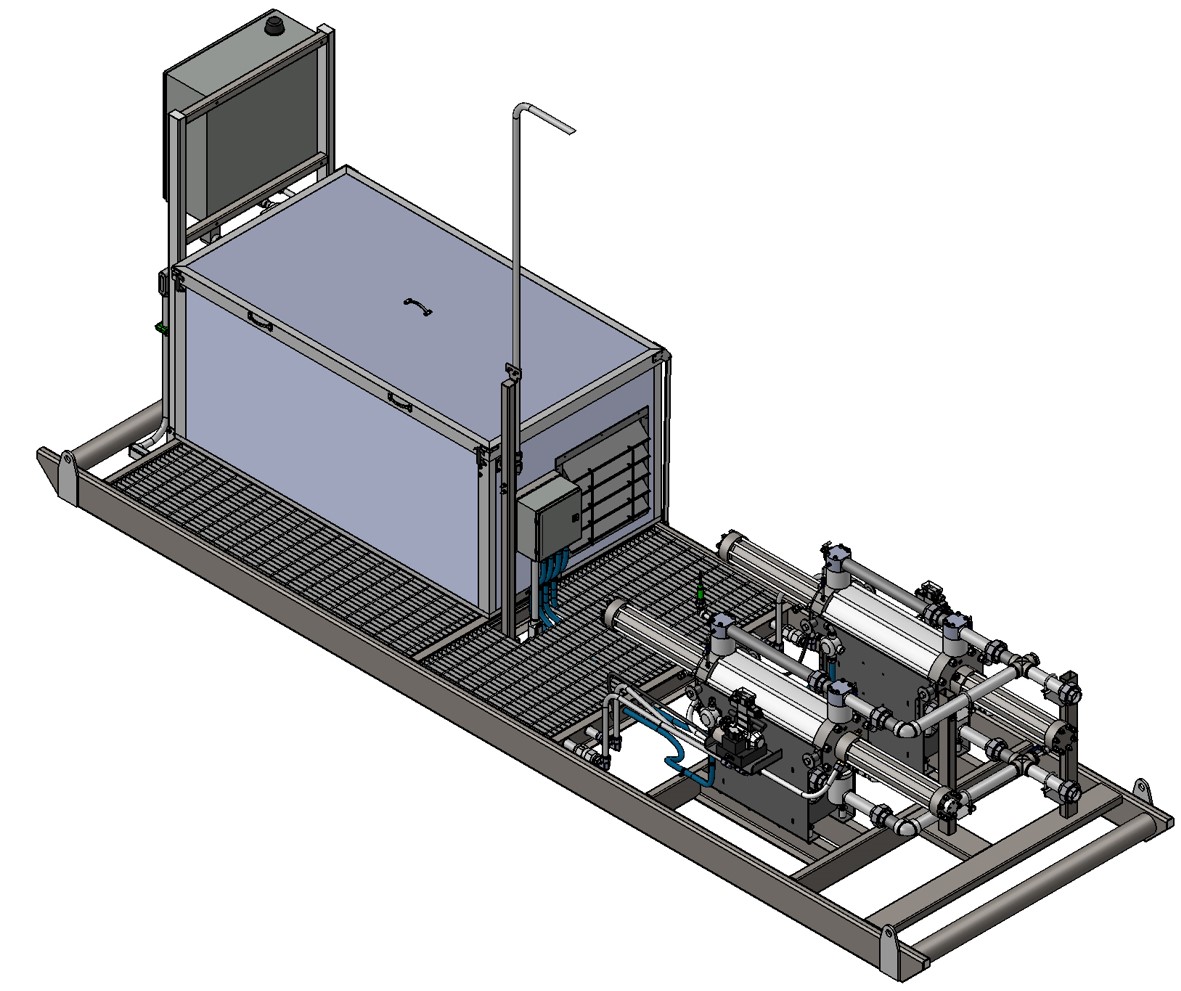
COMPRESSION CYLINDER
LOW PRESSURE
1020
10" (25.4 cm)MEDIUM PRESSURE
1022
10" (25.4 cm)
MAX ΔP
LOW PRESSURE
190 psi
1069 kPaMEDIUM PRESSURE
225 psi
1551 kPa
CAPACITY
Suction @ 20 psi
LOW PRESSURE
412 mscf/d
11667 m3/dMEDIUM PRESSURE
322 mscf/d
9118 m3/d